Think of work order as the engine that drives your maintenance operation. They’re the power behind your team’s effectiveness, propelling work from point A to point B. Work orders are an essential component of fleet management because fleet managers must govern processes before developing fleet maintenance management. Improving the work order process improves the efficiency of fleet maintenance activities; having an optimised work order may be a beneficial alternative for a corporation.
Fleet managers fail to pay attention to every minute but the critical tasks, such as regular vehicle maintenance and servicing, and these simple mistakes can result in compliance failure, lapses, breakdowns, and excessive operating expenditures. These challenges may be readily overcome by adding work order management with a link to technology automation into the company’s existing fleet maintenance operations. As a result, it is vital to understand that work order management is the foundation of every successful maintenance plan.
So, what is a work order?
What Is a Work Order?
A work order is essentially a formal request for maintenance, repair, or operational tasks. This covers all the info you need about the job: what needs to be done, who’s responsible, what we’re aiming for, and how to do it. Work orders help keep things running smoothly and make it easier to handle your tasks and workflow efficiently.
They can be generated through service request forms submitted by staff, customers, or tenants, or automatically created via Work Order Management software, such as a Computerized Maintenance Management System (CMMS). Using CMMS software enhances the work order process by providing technicians with additional resources like checklists, access to documents, images, and more. Furthermore, work orders also help in capturing labor expenses, materials from inventory, spot buys, and other costs incurred during the job.
What Is Work Order Lifecycle?
Every maintenance work order goes through a lifecycle comprised of three primary phases: creation, completion, and recording. Each of these phases is further broken down into six steps, ensuring that maintenance tasks progress smoothly and do not get stuck in any one phase, preventing them from becoming a backlog.
How Do Different Industries Use Work Order Management?
Work order management serves various industries, each adapting the concept to its specific needs:
- Manufacturing: Manufacturing industries utilize work order management software for maintenance applications. Maintenance technicians receive work orders to repair machines and perform preventive maintenance. These work orders may be created manually when equipment requires repair or automatically at specified intervals for preventive maintenance tasks. The work order itself contains documentation and inspection checklists, recording the technician’s actions and observations.
- Housing: In the housing industry, work order management software is used to create maintenance and repair requests. Tenants and staff can submit work requests, ranging from simple tasks like unclogging a toilet to complex projects like building new walls. This software streamlines scheduling and assigns tasks to the appropriate parties, such as plumbers, maintenance personnel, or pest control agencies.
- Contractors: Contractors use work order management software to manage customer requests for products or services. A work order may include pricing, required materials, schedules, and locations for carrying out the service. Upon completion, the contractor sends the work order back to the customer, serving as both a labor and materials log and a customer invoice.
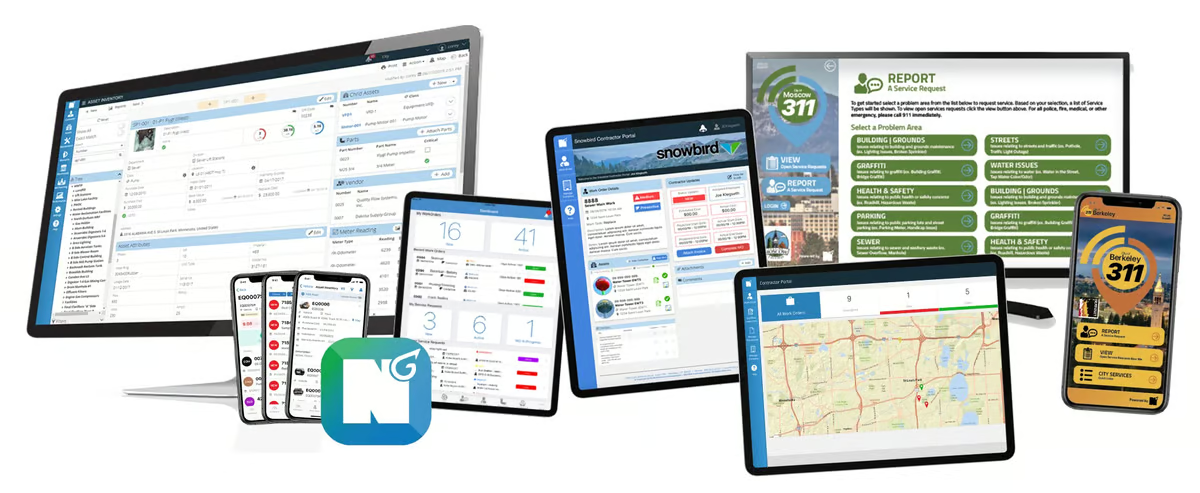
Ready to Learn How CMMS Works?
If you’re looking for a way to make maintenance easier, CMMS software might be just what you need.
Learn More About What is CMMS
What Should Be in a Work Order?
When creating a work order, it’s easiest to work from a template. The most common items to include in a work order are:
- Task description: A clear and concise description of the maintenance task.
- Requestor’s name or party: The person or entity requesting the work.
- Estimated completion time: The expected timeframe for completing the task.
- Responsible party: The individual or team responsible for executing the task.
- Task location/asset: The specific location or asset where the work is to occur.
- Prerequisites: Any requirements for completing the task, such as skills, tools, parts, or other resources.
Types of Work Orders
Work orders come in several types, each suited to different scenarios and requirements:
- General Work Order: These work orders cover maintenance tasks that don’t fall into specific categories like preventive maintenance, inspection, emergency maintenance, or corrective maintenance. General work orders may include setting up new equipment, decommissioning unused equipment, or painting.
- Preventive Maintenance Work Order: Preventive maintenance work orders involve scheduled routine maintenance aimed at preventing costly equipment failures and unplanned downtime. These work orders include details like resource requirements, instructions, checklists, and task notes, and they are typically scheduled at specific intervals.
- Inspection Work Order: Inspection work orders are used to schedule audits or inspections of assets based on predetermined time intervals. During an inspection, technicians assess asset condition and may create new work orders to address identified problems.
- Emergency Work Order: Emergency work orders are generated when unplanned asset breakdowns require immediate repair. They are used to record and track reactive maintenance activities. Technicians include information about the root cause of the unexpected breakdown, the performed maintenance work, and preventative measures in these work orders.
- Corrective Maintenance Work Order: Corrective maintenance work orders are created when technicians identify issues during other work order tasks, such as preventive maintenance, inspection, general, or emergency work orders. These orders are planned and scheduled to resolve identified issues, which may involve repair, replacement, or restoration of equipment or parts.
Benefits of Work Order Management
Work order management offers numerous benefits, including:
- Organized Work Requests: Preventing tasks from being overlooked and ensuring all maintenance requests are addressed.
- Scheduled Work: Efficiently planning and scheduling maintenance tasks for convenient completion.
- Labor and Expense Control: Managing labor expenses and equipment costs to keep maintenance within budget.
- Equipment Availability: Maximizing equipment uptime and performance through timely maintenance.
- Cost Management: Controlling and reducing maintenance-related costs.
- Increased Productivity: Enhancing employee productivity and efficiency.
- Preordering Supplies: Ordering necessary supplies and materials in advance to avoid delays.
- Improved Customer Service: Meeting customer expectations through timely and efficient service.
- Reduced Paperwork: Minimizing paperwork and streamlining documentation.
- Maintenance Backlog Reduction: Decreasing the backlog of pending maintenance tasks.
- Safety Improvement: Enhancing safety practices in maintenance operations.
- Compliance: Ensuring compliance with company, state, and federal regulations.
- Faster turnaround time: An efficient work order system can decrease turnaround times through quicker work completion as greater transparency enables managers to spot and address maintenance-related issues in due time.
- Reduced downtime: Poor management of work orders can result in overlapping demands on equipment and labor at times, and could also lead to idle resources otherwise. The ability to clearly and easily manage resources ensures optimum utilization, resulting in decreased downtime.
- Increases Asset Lifetime: Work order software allows managers to schedule the use of assets and allocation of resources to maintain load-sharing among all resources. Apart from making the best use of the assets, this prevents the over-use of one particular resource, thereby extending its overall lifetime while reducing any added overhead costs due to wear and tear.
- Improved quality control: By using work order software to communicate work orders, the facilities manager can ensure better outcomes as using such platforms greatly increases the likelihood that instructions are clear, easily accessible, received, and executed on time. The tracking tools allow for constant monitoring of key performance areas which provide a mechanism for enforcing adherence to quality standards and increasing employee accountability.
These benefits collectively result in increased efficiency, productivity, safety, compliance, and cost reduction in maintenance operations.
The Work Order Process
Effective work order management follows a structured process with several phases:
Phase 1: Task Identification
In the first phase, individuals or organizations identify maintenance tasks that need to be completed. Tasks can fall into 2 categories: planned maintenance, where jobs are identifiable in advance, and unplanned maintenance, where initial assessment is required to define the scope and specifics of the job.
Phase 2: Work Request Submission
Managers document maintenance issues in a work order request form, which is then submitted to the maintenance department for review and approval. Work requests can originate from various sources, including tenant requests and preventive maintenance audits.
Phase 3: Work Request Evaluation
Upon submission, the maintenance department evaluates work requests. This involves reviewing task details, determining the department’s capability to complete the work, and assessing personnel and resource requirements. If approved, the work order request is converted into a work order.
Phase 4: Work Order Creation
After approval and allocation of necessary materials, equipment, and staff, a work order is created. It includes complete task details, company contact information, and completion deadlines. Prioritization within the workflow is also determined during this phase.
Phase 5: Work Order Distribution and Completion
In this phase, the team or supervisor assigns tasks to qualified maintenance technicians, who follow the provided checklist to complete the tasks within the specified timeline. In facilities using Computerized Maintenance Management System (CMMS) software, work orders are automatically assigned to technicians.
Phase 6: Work Order Documentation and Closure
Maintenance technicians document their work and close the work order once all tasks are completed. Documentation should include time spent on each task, materials and equipment used, images of the work, and any relevant notes or observations. A manager may review and sign off on the completed work order, guiding the next steps as necessary.
Phase 7: Work Order Review and Analysis
Regularly reviewing completed work orders offers valuable insights into maintenance operations. This analysis helps identify opportunities for process improvement, allowing maintenance teams to continuously refine and enhance their work order process.
Work Orders vs Service Requests
What’s the difference between a work order and a service request?
A service request is a submission from staff or customers to request maintenance work on an asset, while a work order is authorization from a maintenance planner to execute maintenance tasks. When service requests are submitted and approved, work orders are created.
Work Order vs Purchase Order
What’s the difference between a work order and a purchase order?
Work orders and purchase orders are distinct concepts. A work order is used to assign maintenance tasks, while a purchase order authorizes the purchase of goods and services from external vendors. For instance, a manufacturing company may use work orders to schedule equipment inspections and purchase orders to request the purchase of raw materials from external suppliers.
Best Practices for Managing Work Orders
Effective work order management relies on best practices to ensure optimal performance:
- Establish Maintenance Goals and KPIs: Define maintenance goals and KPIs to guide your work order management process and ensure your team adheres to established best practices.
- Define Roles and Responsibilities: Clarify roles in the work order process to streamline task execution, avoid duplication, prevent unauthorized work, and enhance communication.
- Choose Automation Triggers: Implement automation based on triggers such as breakdowns, time-based schedules, event-based events, usage-based thresholds, and condition-based indicators. A CMMS can automate work orders based on these triggers, facilitating early issue resolution.
- Continuously Analyze and Improve: Work order management is a continuous process of refinement and adaptation. A robust CMMS can help your team adhere to established standard operating procedures and best practices, improving productivity and maintenance outcomes.
How do Work Orders Improve Maintenance?
Work orders play an important role in enhancing maintenance operations in several ways:
- Data Collection: Work orders capture comprehensive data on work completion, resource utilization, and task execution, facilitating performance monitoring, trend analysis, and continuous improvement.
- KPI Generation: Work orders enable the generation of key performance indicators (KPIs) such as schedule compliance, MRO (Maintenance, Repair, and Operations) expenditure, and MTBF. These KPIs provide valuable insights into maintenance performance.
- Schedule Compliance: Work order software can help calculate KPIs like schedule compliance by assessing the percentage of scheduled work completed within a specified timeframe.
- MRO Expenditure: Effective work order management allows organizations to track the cost of materials and equipment used in maintenance tasks. Increasing costs for specific items can indicate recurring failure modes or frequent asset breakdowns, prompting improvements in preventive maintenance processes.
- MTBF Analysis: Work order data helps in calculating the mean time between failures (MTBF), which measures the average time between failure events on specific assets. Monitoring assets with frequent reactive maintenance tasks reveals opportunities to enhance preventive maintenance procedures.
Using a CMMS for Work Order Management
Work orders are at the core of a successful maintenance program. Leveraging a CMMS helps organizations keep track of labor, projects, and resources, making it easier to control work backlogs and upcoming tasks. An effective CMMS can help maintenance teams reduce unplanned asset downtime, save costs, and scale their operations. To optimize work order management, consider implementing a reliable computerized maintenance management system.
Work Order Management With NEXGEN
A good CMMS will help your team adhere to established SOPs and best practices, leading to enhanced productivity and better maintenance outcomes. Ready to optimize your word order management with NEXGEN?