What Is Predictive Maintenance?
Predictive maintenance (PdM) is a maintenance approach that leverages data analysis tools and techniques to identify potential faults in equipment, assets, and processes. By using PdM, you can proactively address these issues before they escalate into failures.
The primary goal of predictive maintenance is to minimize the frequency of unplanned reactive maintenance while avoiding excessive costs linked to excessive preventive maintenance. By strategizing with your maintenance, you can strike the optimal balance between preventing failures and avoiding unnecessary maintenance activities.
How Does Predictive Maintenance Work?
Before installing sensors to help monitor your assets for the need for maintenance, it is important to monitor an asset’s conditional baseline. This serves as a reference point, or “control,” against which any deviations can be compared. Once you start collecting conditional data, the process becomes straightforward. Whenever a piece of equipment operates outside of normal parameters, the sensors activate your predictive maintenance protocol. Typically, this generates a work order in your CMMS (Computerized Maintenance Management System), which is then assigned to technicians who can execute the necessary repairs.
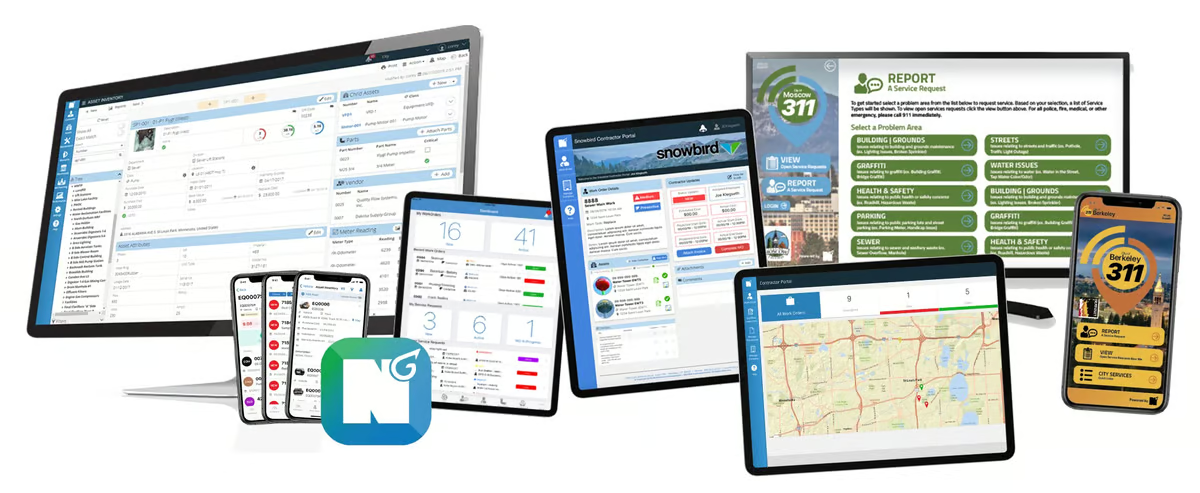
Ready to Learn How CMMS Works?
If you’re looking for a way to make maintenance easier, CMMS software might be just what you need.
Learn More About What is CMMS
Why Is Predictive Maintenance Important?
By implementing predictive maintenance strategies, several significant benefits can be achieved. This approach to asset management enables compliance with safety regulations, facilitates preemptive corrective actions, and extends the lifespan of assets. By anticipating potential failures and accurately predicting when they are likely to occur, proactive measures can be taken beforehand to ensure critical failures are stalled or prevented. These measures may involve conducting preemptive investigations, making necessary adjustments to maintenance schedules, and performing timely repairs. This proactive approach not only enhances safety and regulatory compliance but also minimizes downtime and maximizes the efficiency of asset management.
Types of Predictive Maintenance
Vibration Analysis
This particular type of analysis is widely recognized as the preferred method for predictive maintenance in manufacturing plants that house machinery with high rotation rates. Its longevity in the field has made it a cost-effective option compared to other condition-based techniques. Aside from detecting issues like looseness, vibration analysis is also capable of identifying problems such as imbalance, misalignment, and bearing wear.
Acoustic Analysis (Sonic)
Acoustic analysis, a cost-effective approach applicable to both low- and high-rotating machinery, has gained popularity among lubrication technicians. Unlike vibration analysis, which aims to identify the causes of equipment failure by measuring vibrations at specific frequencies and monitoring trends, acoustic bearing analysis serves a different purpose. It is primarily geared towards proactive lubrication measures, providing valuable insights to lubrication technicians. As described in this article by Machinery Lubrication, this method utilizes sound-based analysis to optimize lubrication practices and enhance machinery performance.
Acoustic Analysis (Ultrasonic)
Sonic acoustic analysis treads the line between preventive and predictive maintenance practices, whereas ultrasonic acoustic analysis is exclusively employed for predictive maintenance purposes. By detecting and analyzing sounds within the ultrasonic range, this method is capable of identifying machine friction and stress-related noises. Consequently, ultrasonic acoustic analysis is applied to both electrical and mechanical equipment, especially those that emit subtle sounds. Supporters argue that this type of analysis provides a superior prediction of imminent breakdowns compared to vibration or oil analysis techniques. Its ability to capture and interpret ultrasonic signals positions it as a valuable tool for enhancing maintenance strategies and preventing costly equipment failures.
Infrared Analysis
Infrared analysis is a versatile and effective technique that can be applied to various types of assets without being reliant on factors such as rotational speed or loudness, which makes it a suitable tool for predictive maintenance. One of its primary advantages is its cost-effectiveness in identifying potential issues by analyzing temperature patterns. Infrared analysis proves particularly valuable in detecting and addressing problems related to cooling systems, airflow, and even motor stress. By utilizing this method, maintenance teams can proactively identify and resolve issues, leading to optimized asset performance and the prevention of costly breakdowns.
When Should I use Predictive Maintenance?
To help you decide whether or not your organization should use predictive maintenance for a specific application, see the table below.
Suitable Applications | Unsuitable Applications |
Applications with crucial operational functions | Applications lacking critical functions |
Applications with failure modes that can be economically predicted through regular monitoring | Applications lacking predictable failure modes |
Who Uses Predictive Maintenance?
In the world of maintenance management, predictive maintenance tools and asset management systems are commonly employed by maintenance managers and their teams. These tools and systems serve the purpose of monitoring potential equipment failure and facilitating maintenance tasks. By leveraging predictive maintenance tools, managers can proactively identify signs of impending equipment failure, allowing them to plan and schedule necessary maintenance activities promptly. Additionally, asset management systems provide a comprehensive platform for organizing and tracking maintenance tasks, ensuring efficient workflow and optimal equipment performance. Together, these tools and systems contribute to effective maintenance management, enhancing equipment reliability and minimizing downtime.
How Is Predictive Maintenance Used?
If a crucial asset in your organization were to break down, processes would halt until repairs or replacements were completed, which could take lengthy amounts of time. However, with an asset management system in place, you can monitor specific aspects of the asset, like temperature, and use that data to preemptively plan maintenance. For example, if the temperature of a hypothetical pump exceeded a predefined threshold, it would indicate that the pump needs maintenance and is at risk of imminent failure. In response, you can proactively schedule preventive maintenance, addressing the issue before it escalates and causes a complete breakdown that halts business processes.
Predictive maintenance software plays a vital role in this scenario by continuously monitoring the machines and analyzing data using predictive analytics. When the software identifies signs of stress or potential issues, it promptly notifies the maintenance team. This notification allows the team to plan and execute preventive maintenance activities, effectively reducing costly downtime. By leveraging predictive maintenance software, organizations can minimize the impact of equipment failures, optimize maintenance schedules, and ensure uninterrupted production processes.
How to Begin Using Predictive Maintenance
The process of implementing predictive maintenance typically involves several key steps, beginning with the presentation of Return on Investment (ROI) cases to management. Following this, maintenance staff and machine operators undergo training on the proper utilization of predictive maintenance technology. Once these initial steps are completed, your organization can truly begin to use predictive maintenance in its daily operations.
- Establish baselines: The maintenance team sets acceptable condition limits for assets by using sensors. These limits serve as benchmarks for monitoring asset health and performance.
- Install sensors: The relevant sensors are then installed on the corresponding assets. For example, a vibration meter may be affixed to a mechanical asset with gears, while a temperature sensor might be attached to a boiler.
- Connect devices to software: The Internet of Things (IoT) devices and aforementioned sensors are connected to a Computerized Maintenance Management System (CMMS) or a remote dashboard. This enables the collection and analysis of data taken from the assets by the sensors.
- Schedule maintenance: Once the condition of an asset meets the baseline established in step one, work orders are automatically triggered by the CMMS or manually fired by whoever is supervising the PdM dashboard. This ensures timely maintenance actions based on data-driven insights gathered from the sensors.
By following these steps, organizations can effectively implement predictive maintenance, enabling proactive maintenance actions and optimizing asset reliability and performance.
Benefits of Predictive Maintenance
Though both preventive and predictive maintenance is leagues better than reactive maintenance, predictive maintenance offers significant advantages over preventive maintenance by ensuring that equipment is only taken offline for regular maintenance only when necessary rather than relying on a time-based approach. This reduces both the overall time and cost spent on equipment repairs and replacements.
When practiced effectively, predictive maintenance allows maintenance activities to be carried out precisely when they are needed. This results in several cost-saving factors:
- Minimization of equipment downtime during maintenance.
- Reduction in production hours lost due to maintenance activities.
- Decrease in the expenditure on spare parts and supplies.
Moreover, predictive maintenance programs have been proven to deliver a substantial return on investment (ROI) with a potential tenfold increase by achieving:
- A reduction in maintenance costs ranging from 25% to 30%.
- A significant decrease in breakdowns by 70% to 75%.
- A considerable reduction in downtime by 35% to 45%.
However, these savings come with certain considerations. Some condition monitoring techniques utilized in predictive maintenance can be costly, and their effective implementation requires specialized personnel with expertise in data analysis. If you are considering predictive maintenance, we recommend you take stock of your organization’s budget and needs.
Disadvantages of Predictive Maintenance
Compared to preventive maintenance, the cost of the condition monitoring equipment required for predictive maintenance is generally high. The level of skill and experience needed to accurately interpret state monitoring data are also high. In combination, these factors can mean that monitoring the condition entails high upfront costs. Some companies hire condition-monitoring contractors to minimize the initial costs of a condition-monitoring program.
Not all systems have faults that can be repaired more cost-effectively through preventive maintenance or a run-to-failure maintenance strategy. When deciding if predictive maintenance is best for a particular plant, you should decide at your own discretion. Techniques such as reliability-based maintenance provide a systematic way of determining if predictive maintenance is a good option as a maintenance strategy for the particular plant of interest.
Predictive Maintenance vs Preventive Maintenance
What is the difference between predictive maintenance and preventive maintenance? For a breakdown, see the table below.
Predictive Maintenance | Preventive Maintenance |
Uses predictive maintenance technology to resolve potential problems and plan corrective actions before a fault occurs | Usually uses planning software to inform teams or individuals about upcoming equipment maintenance. For example, when a car travels a set number of miles, the driver is notified about the need for an oil change. |
Improves the overall efficiency of the warehouse, as machine parts do not fail and are not replaced too soon | Provides you with good indicators of the performance and the status of the assets Predictive Maintenance Examples |
Doesn’t usually require machine downtime, and if it does, it’s usually brief | Often requires machine downtime |
Predictive Maintenance Examples
Oil and Gas Sector
The process of oil drilling subjects assets to significant wear and carries inherent risks and dangers in the event of failure. However, the implementation of real-time monitoring, specifically tracking changes in oil temperature and gearbox speed in drilling equipment, has revolutionized maintenance practices. Predictive maintenance has played a vital role in enhancing safety measures and reducing maintenance costs by an impressive 38%.
Automotive Industry
In the realm of assembly lines, spot-welding guns tirelessly perform around 15,000 spot welds daily. By connecting and collecting operational data from welding guns worldwide, automotive manufacturers can amass millions of data points. This wealth of information provides unprecedented accuracy in predicting the condition and status of these crucial assets.
Domestic Appliance Manufacturing
The production process for dryers involves measuring vibrations resulting from drum rotation. These measurements have proven invaluable in predicting potential malfunctions or breakdowns. By leveraging predictive maintenance, manufacturing defects have been curtailed by 33%, leading to a substantial 27% reduction in consumer maintenance costs.
Railroad Asset Management
The emergence of “voids,” empty spaces forming beneath tracks, poses a significant risk of delays or even derailments. To address this, innovative cab-based monitoring systems have been introduced. These systems can detect various variables as they traverse the rails, enabling improved void detection and, consequently, enhanced customer safety.
Steel Industry
Anomaly detection techniques have been employed to gather real-time readings of vibration, rotational speed, and electrical current in cold-rolling equipment used in steel processing. This application has brought about a remarkable 60% improvement in equipment lifetime while significantly reducing losses attributed to downtime and delays.
Final Thoughts
Predictive maintenance might not be suitable for every organization, especially those that have not yet implemented planned maintenance activities. However, for larger organizations that have surpassed the limitations of traditional maintenance approaches and possess additional budgets, predictive maintenance can offer a return on investment that transforms the maintenance department into a catalyst for cost savings and increased profitability.
Protect Your Assets with Predictive Maintenance
Interested in hearing about NEXGEN’s Predictive Maintenance module? Click the button below to see NEXGEN in action.