Preventive maintenance is one of those things that sounds simple in theory but can get overwhelming fast when you’re juggling schedules and work orders. If you’ve ever found yourself wondering how to keep up, you’re not the only one. A lot of businesses struggle to set up a system that works, and it often leads to equipment issues, costly downtime, and extra headaches.
But here’s the good news- you don’t have to stay stuck in the chaos. This guide will walk you through how to create a preventive maintenance schedule that works, keeping your equipment in top shape while saving you time, money, and stress.
What is a Preventive Maintenance Schedule?
Preventive Maintenance Schedule is a strategic plan designed to keep your equipment, machines, and facilities running smoothly. Instead of waiting for things to break down, regular check-ups and maintenance tasks are scheduled to prevent unexpected issues. These tasks can range from simple actions like cleaning and lubricating to more involved processes like replacing parts or updating software. The frequency of these tasks depends on the equipment’s type and usage, as some may require daily attention, while others might only need annual check-ins.
In short, a preventive maintenance schedule makes sure you’re proactive about maintenance, helping extend equipment lifespan and reduce downtime.
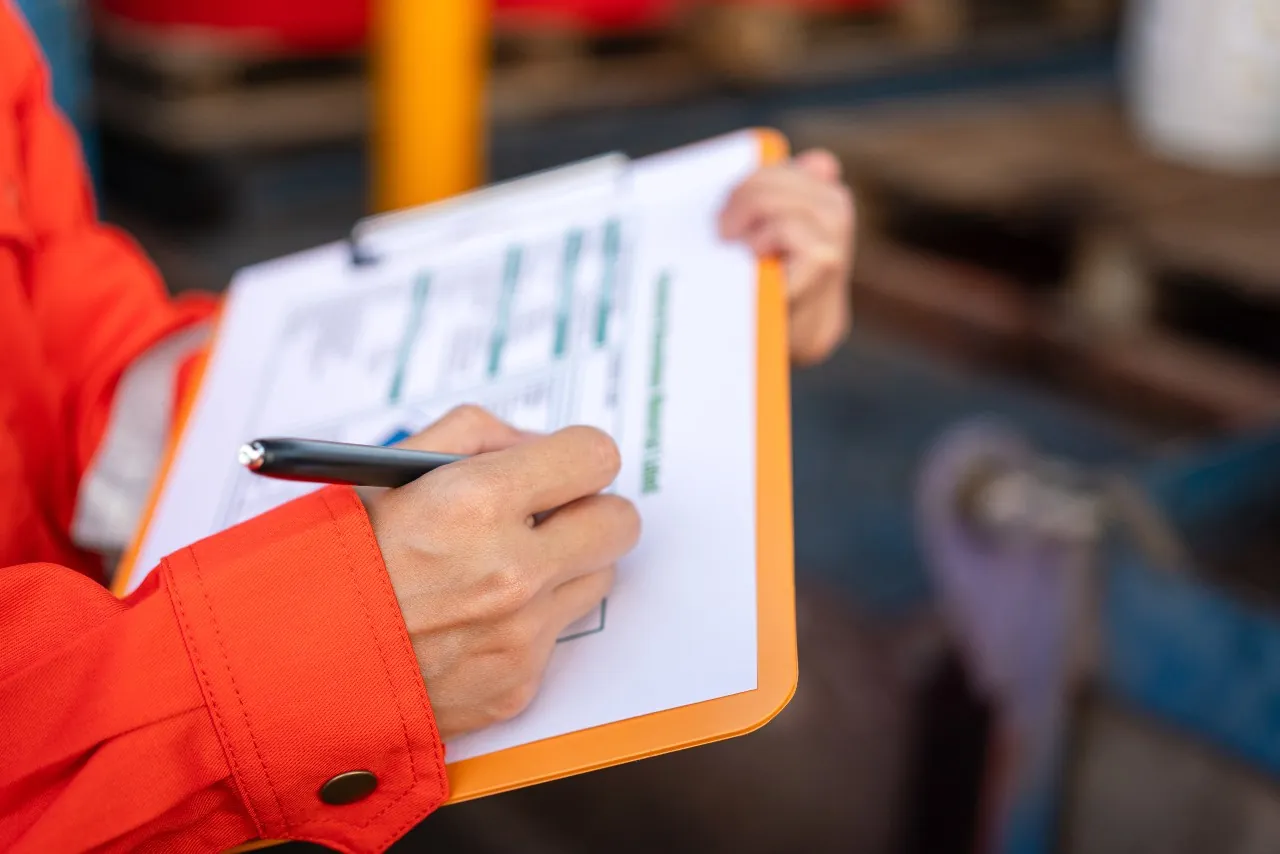
Build an Effective Preventive Maintenance Checklist
Learn the essential steps to design a checklist that keeps your assets in top condition.
Why is a Preventive Maintenance Schedule Important?
It is essential for keeping things running smoothly and avoiding big problems down the road. Here’s why it’s so important:
- Keeps Things Running Reliably: Regular check-ups help catch potential problems before they turn into costly breakdowns. It’s like going to the doctor for a check-up, so that small issues get spotted early, and your equipment keeps working as it should.
- Saves Money Long-Term: Preventing breakdowns means fewer surprise repairs, which can be expensive. With a good maintenance plan, you’re reducing the chances of major issues, saving your business a lot in the long run.
- Extends Equipment Lifespan: Routine maintenance helps keep your equipment in top condition, so you won’t need to replace it as often. That means you’re getting more mileage out of your investments.
- Keeps People Safe: Well-maintained equipment is safer. Regular inspections help prevent accidents, making sure that your workplace stays a safe environment for everyone.
- Boosts Productivity: By planning for maintenance, you avoid unexpected downtime. This means your team can keep things moving without unnecessary interruptions, which leads to better overall efficiency.
Different Types of Preventive Maintenance Schedules
Creating a preventive maintenance schedule involves 2 primary approaches: fixed and floating. Each has its strengths, so let’s break them down.
-
Fixed Preventive Maintenance Schedule
A fixed PM schedule is like following a strict routine. You set specific times or usage intervals for when tasks need to be done, no matter what happened before. If you’ve got a vehicle that needs an oil change every 3,000 miles, it’s non-negotiable, as once that odometer hits 3,000, it’s time for that oil change, whether it took a week or a month to get there. Fixed schedules ensure nothing slips through the cracks because it’s always on the calendar.
-
Floating Preventive Maintenance Schedule
A floating PM schedule is more flexible, adjusting based on when the last task was completed. Imagine you have equipment that needs servicing every 100 hours of operation, but life happens, and you don’t get to it until hour 120. With a floating schedule, the clock resets at 120 hours, and the next maintenance won’t be due until 220 hours. This makes floating schedules ideal for tasks that depend on actual usage rather than rigid timelines.
Both methods have their advantages- fixed schedules keep you on a strict routine, while floating schedules offer flexibility based on real-time usage. Choosing the right approach depends on the specific demands of your equipment and how closely you need to stick to a routine
How to Create a Preventive Maintenance Schedule?
Here are 6 key steps to guide you through the process of building an effective preventive maintenance schedule:
-
Start with the Essentials
Not all your equipment needs the same level of attention. Focus on the heavy hitters first: the machines that are most critical to your operations or the ones that would cost you big if they failed.
Pro tip: Do a quick ‘criticality analysis’. Ask yourself, “What would happen if this machine stopped working?”. If the answer is chaos (or major repair bills), that’s a sign it needs to be at the top of your list.
-
Figure Out When Maintenance Makes Sense
Too much maintenance? Waste of time. Not enough? Well, we all know what happens then- unexpected failures. Find the sweet spot by:
- Checking Manufacturer Recommendations: They’ve designed the equipment, so they usually know best.
- Looking at the Past: Historical data from breakdowns can give you clues on how often to schedule maintenance.
- Talking to Your Team: Your operators and technicians can offer great insights into the quirks of your machines and the warning signs they’ve seen.
-
Prioritize Maintenance Tasks
Once you know the ideal intervals, it’s important to prioritize maintenance tasks. Focus on tasks that have the biggest impact on equipment performance and safety. Routine tasks such as inspections, cleaning, and lubrication should be given priority.
-
Make Responsibilities Clear
It’s great to have a schedule, but who’s going to do the work? Assign tasks to your team clearly, so there’s no confusion about who’s responsible for what. Everyone should know what’s expected of them and by when.
-
Keep Track of Everything
After each task is completed, make sure it’s documented. This helps you adjust your schedule if needed. If you see certain equipment is always needing repairs, that might be a sign to tweak the schedule or invest in a replacement.
Pro tip: Use checklists to keep everything organized. A completed checklist shows that everything has been handled, and you have a record for future reference.
-
Check How It’s Going
Once your schedule is up and running, don’t just leave it. Review it regularly to see what’s working and what isn’t. Metrics like Mean Time Between Failures (MTBF) or Preventive Maintenance Compliance (PMC) can help you see how effective your maintenance program is, and where you can improve.
Common Preventive Maintenance Schedule Options
Scheduling by Dates
This is the most common approach to the preventive maintenance schedule. Scheduling by dates offers the flexibility of specifying work order frequency. Although setting up is easy, the challenge with this is that your maintenance schedule may be less optimal than needed. For instance, it may be too early in certain cases where the machine is not used frequently due to a shutdown or late where the machine runs for longer hours than normal, increasing the risk of equipment breaking down.
Scheduling by Meter Readings or Equipment Usage
This involves keeping track of the machine runtimes that will then form a basis for your preventive maintenance schedule. Take an example of a vehicle that can be scheduled for an oil change after 3000 miles or a widget-making machine that can be scheduled for maintenance after a thousand widgets. Although this approach may produce a more optimal maintenance schedule, it involves more work as meter readings must be taken manually. Even then, you may also work with estimated readings.
Scheduling on a Basis of Another Task or Work Order
Here, the maintenance tasks are scheduled days after the completion of the last maintenance task work order. This is especially useful when there is a need to chain work orders (e.g. a maintenance task involving two separate tasks that need to be undertaken by different sub-contractors). Tasks can also be scheduled based on prior completion (e.g. scheduling a preventive maintenance task to be done in 30 days following the completion of the previous maintenance).
Scheduling Based on an Alarm Condition
This scheduling option lets you define an external condition such as an alarm which means preventive maintenance needs to be done. A good example would be a machine that has an overheating condition and requires constant lubrication of its bearings. This also covers maintenance requests as well as alarms that are scheduled with the use of condition monitoring or even predictive maintenance systems. These may be external specialized systems that are different from maintenance management software which is responsible for analyzing equipment data before flagging potential issues or predicting when a maintenance issue is due. These systems raise a notification that is similar to an alarm that the CMMS software may use in scheduling multiple maintenance tasks albeit on separate enterprise assets.
Factors That Can Affect a Preventive Maintenance Schedule
Here are some key factors that can disrupt your preventive maintenance schedule:
- Poor Team Communication: Without clear communication, teams can miss important details like equipment status or task priorities. This leads to confusion, redundancies, or delays. Use real-time communication tools to keep everyone on the same page.
- Inefficient Maintenance Inventory Management: If spare parts or tools aren’t available when needed, tasks get delayed, creating a backlog. Digitizing your inventory can help prevent shortages and avoid unplanned downtimes.
- Lack of In-House Skills for Specialized Tasks: Certain maintenance tasks may require expertise that your in-house team lacks. This can lead to outsourcing delays and increased costs. Training staff or smart outsourcing is key to staying on track.
- Inconsistent Maintenance Practices: When maintenance tasks aren’t standardized, mistakes happen. Consistency ensures that equipment receives proper care. Establishing clear SOPs helps technicians follow the same reliable steps every time.
Preventive Maintenance Scheduling with NEXGEN
Tackling preventive maintenance doesn’t have to be a headache. NEXGEN got your back.
Instead of trying to balance too much or too little maintenance on your own, NEXGEN helps you get it just right. With deep insights into critical metrics like Mean Time Between Failure (MTBF) and Mean Time To Repair (MTTR), you can fine-tune your schedule and keep things running smoothly.
Schedule a demo and see how NEXGEN can transform your workflow!
NEXGEN Makes Scheduling Easier
NEXGEN’s CMMS software makes sure you’re squeezing the most value out of every preventive task. Ready to simplify your maintenance?
FAQs
-
What should be included in a preventive maintenance schedule?
A preventive maintenance schedule should clearly outline what tasks need to be done, who is responsible for them, how they should be performed, and when they should be completed.
-
How often should a preventive maintenance schedule be reviewed and updated?
A good starting point is to review the PM schedule annually. However, more frequent reviews, like quarterly or semi-annually, may be necessary for high-risk industries or critical equipment. Always update the schedule if there are significant changes in operations or equipment conditions.
-
What are the benefits of using preventive maintenance scheduling software?
Preventive maintenance scheduling software ensures that assigned technicians have all the information they need to complete their tasks. Automated scheduling also helps prevent missed work by sending timely reminders, ensuring that no critical maintenance tasks fall through the cracks.