Every company must have a stringent maintenance strategy in place—this is especially true for asset-intensive businesses—to achieve efficiency and higher profits. The maintenance strategy you employ in the facility will have a tremendous impact on the company’s bottom line. Unfortunately, quite a few maintenance managers have a difficult time choosing the appropriate strategy, or worse, they completely overlook the approach altogether.
It is important to have Enterprise Asset Management software in place while implementing a strategy to track work and schedule. There are 4 basic types of maintenance: Reactive, Reliability-Centered, Preventive, and Predictive. Choose the one that works best for the assets in question.
Do not wait until a component fails to take the necessary action to repair or replace it. All assets require periodic maintenance to continue running efficiently, which is why you must find the appropriate balance of maintenance approaches to minimize asset downtime and repair costs while maintaining a safe environment for workers.
What is a Maintenance Strategy?
A maintenance strategy is a structured plan that helps companies keep their equipment running smoothly while reducing downtime and managing repair costs. It outlines how maintenance activities should be carried out to ensure that machines, tools, and infrastructure remain in good working condition, allowing factories and facilities to operate efficiently.
A well-planned maintenance strategy is an important part of asset management. It helps businesses take care of the equipment and systems that support daily operations and production. By having a clear approach to maintenance, companies can avoid unexpected breakdowns, extend the life of their assets, and create a safer work environment.
With advancements in technology, businesses now have access to a variety of maintenance approaches. The rise of data and analytics has made it possible to track equipment performance in real-time, predict when repairs will be needed, and adopt more precise maintenance methods. From routine inspections to predictive maintenance using smart sensors, companies can choose a combination of strategies that best fit their needs and industry requirements.
Key Considerations for Developing a Maintenance Strategy
Developing an effective maintenance strategy requires a focus on comprehensive asset data management. This includes maintaining detailed equipment history, implementing condition monitoring techniques, and effectively tracking work orders. Continuous improvement plays a vital role, with regular evaluations and feedback loops helping refine and optimize strategies.
Technology, particularly computerized maintenance management systems (CMMS), can be leveraged to streamline operations and achieve better asset management outcomes. By prioritizing data-driven decision-making and embracing technological advancements, organizations can enhance their maintenance practices and ensure the longevity and reliability of their assets.
Exploring 4 Maintenance Strategies for Improved Asset Management
- Reactive Maintenance (RM): Reactive maintenance involves addressing equipment failures as they occur. It is a cost-cutting approach where repairs are performed only when assets break down. While it may seem cost-effective initially, relying solely on reactive maintenance can lead to production delays and increased costs in the long term. It is suitable for non-essential or low-cost equipment where replacement is more feasible than repair.
- Preventive Maintenance (PM): Preventive maintenance follows a scheduled plan to proactively service machinery and reduce downtime. By adhering to recommended maintenance intervals, organizations aim to extend the lifespan of their assets. While it can incur the cost of replacing still functional parts, it helps identify and address issues before they result in unplanned downtime. Preventive maintenance is an efficient strategy for preserving medium-priority assets and optimizing repair costs.
- Predictive Maintenance (PdM): Predictive maintenance utilizes condition monitoring and machine learning algorithms to predict and prevent equipment failures. It enables real-time identification of potential maintenance concerns, allowing timely interventions to avoid breakdowns or performance degradation. By adopting predictive maintenance, organizations can significantly reduce unplanned downtime, optimize maintenance schedules, and save costs over time. Although it requires an initial technology investment, the return on investment can be quickly realized.
- Reliability-Centered Maintenance (RCM): Reliability-centered maintenance focuses on analyzing potential failure modes and developing tailored plans to ensure the availability of equipment, regardless of criticality. It aims to maximize reliability by understanding the specific needs of each part and implementing maintenance strategies accordingly. Successful implementation of RCM often requires partnering with experienced professionals to ensure effective execution across the organization’s asset network. RCM is a comprehensive approach to maintenance that prioritizes reliability and aims to minimize costly disruptions.
Strategy | Summary | Cost to Implement | Pros | Cons |
---|---|---|---|---|
Reactive | Address issues as they arise; repairs only after failure occurs. | Low | Suitable for equipment that is not critical or rarely breaks down. | Can result in unexpected downtime and higher repair costs over time. |
Preventive | Perform regular maintenance based on a set schedule, regardless of equipment condition. | Average | Simple to implement and doesn’t require advanced technical knowledge. | Can lead to over-maintenance if schedules aren’t optimized, wasting resources and time. |
Predictive | Monitor equipment condition to perform maintenance only when necessary. | High | Allows timely intervention and provides insights into potential failures, reducing unexpected breakdowns. | Initial setup and equipment monitoring tools can be costly. |
Reliability-Centred | Analyze failure causes to determine the most suitable maintenance approach. | Highest | Offers a highly efficient maintenance plan that extends equipment life and reduces costs if done correctly. | Requires significant investment in training, analysis, and ongoing evaluation. |
Maintenance Strategy Components
A well-planned maintenance strategy helps businesses keep their equipment running smoothly, reduce downtime, and manage costs efficiently. Different elements come together to create a structured approach that extends the lifespan of machinery and minimizes unexpected failures.
-
Computerized Maintenance Management System (CMMS)
A CMMS is specialized software that helps companies keep track of their assets, manage work orders, and plan maintenance activities. It stores detailed information about all equipment, schedules maintenance tasks, and organizes the resources needed for repairs. With a CMMS, businesses can maintain a clear record of past maintenance, analyze trends, and make informed decisions about future servicing.
-
Maintenance Scheduling
Once a company has decided on a maintenance approach that aligns with its operations, creating a structured schedule is the next step. The scheduling process depends on the chosen maintenance strategy:
- Reliability-Centered Maintenance (RCM): The schedule is based on various operational factors and failure patterns.
- Predictive or Preventive Maintenance: Data and equipment performance trends guide maintenance timing and replacement schedules.
- Run-to-Fail Maintenance: Instead of following a structured schedule, this approach accepts that certain components will be replaced only after they fail.
A well-organized maintenance schedule ensures that necessary inspections and repairs take place at the right time, reducing unexpected breakdowns.
-
Condition Monitoring
Condition monitoring involves tracking equipment performance in real-time to determine when maintenance is needed. This method is commonly used in predictive maintenance strategies. Businesses use technologies such as vibration analysis, temperature sensors, and Internet of Things (IoT) devices to collect data. By analyzing this information, maintenance teams can address potential issues before they lead to major failures.
-
Incident Reporting
When equipment malfunctions or breaks down, it is essential to document the incident. Maintenance teams record details about the failure, including what happened, when it occurred, and any immediate actions taken. Keeping track of such incidents allows businesses to identify patterns, improve maintenance planning, and reduce the chances of similar issues happening in the future.
-
Root Cause Analysis
Understanding why equipment fails is just as important as fixing it. Root cause analysis helps maintenance teams identify the underlying reasons behind a breakdown. Instead of just replacing the faulty part, they examine contributing factors such as wear and tear, environmental conditions, or improper usage. This deeper understanding allows companies to implement better maintenance practices and prevent repeat failures.
-
Failure Mode and Effects Analysis (FMEA)
FMEA is a structured approach to predicting how equipment or components might fail, assessing the impact of these failures, and determining how they could affect overall operations. This process helps businesses identify weak points in their maintenance strategy, prioritize risks, and develop plans to minimize disruptions.
NEXGEN Makes Maintenance Easier
With the right maintenance strategy, NEXGEN CMMS software can continue to be a powerful asset in your organization’s maintenance strategy, offering significant benefits for years to come.
Factors to Consider When Choosing a Maintenance Strategy
Every organization has different needs when it comes to maintenance and several factors influence which approach works best. Below are some important considerations that organizations take into account when shaping their maintenance strategies.
-
Budget and Financial Resources
Some organizations have the financial flexibility to invest in advanced maintenance strategies, while others must work within tighter budgets. Many businesses start with basic reactive or preventive maintenance, using in-house staff to handle routine repairs. However, moving to a more advanced approach, like reliability-centered maintenance (RCM) or predictive maintenance, requires additional investment.
These methods often rely on technology such as sensors, monitoring software, and data analytics to track equipment performance. In some cases, upgrading to newer machinery is necessary to take advantage of smart technologies like IoT and machine learning. While these investments can reduce long-term costs and downtime, organizations must weigh them against their available budget.
-
Type of Equipment in Use
The nature of the machinery plays a major role in deciding how to approach maintenance. If an organization relies on inexpensive, easily replaceable equipment, a run-to-failure model may be the most practical choice. In this case, monitoring and repairing might cost more than simply replacing the equipment when it breaks.
On the other hand, if the organization uses complex, high-value machinery that is difficult to replace, a more structured maintenance approach is necessary. Advanced strategies like predictive maintenance or RCM help extend the lifespan of expensive equipment and prevent costly disruptions.
-
Workforce and Staffing Capabilities
No matter how advanced a maintenance strategy is, human expertise is still essential. Trained personnel are needed to monitor equipment, interpret data, and make informed decisions on repairs and replacements. Organizations must assess their staffing levels and technical expertise when choosing a maintenance approach.
If there are enough skilled workers to handle preventive tasks, then regular maintenance schedules may be manageable. However, if staffing is limited, investing in automated monitoring systems and predictive maintenance tools may be a better solution to reduce reliance on manual checks.
-
Condition of Existing Equipment
The current state of machinery is another factor that influences maintenance decisions. If the equipment in use is outdated and prone to frequent breakdowns, it may not be practical to keep investing in repairs. In such cases, allowing older machines to run until failure and gradually replacing them with newer models can be a better long-term approach. Newer equipment often supports advanced maintenance strategies, making it easier to transition to preventive or predictive methods.
-
Industry Regulations and Compliance Requirements
Certain industries have strict safety and compliance regulations that dictate how maintenance should be carried out. Equipment used in sectors like healthcare, aviation, and food production may require frequent monitoring to meet industry standards and ensure safe operation. In such cases, preventive maintenance or RCM becomes necessary to maintain compliance, protect workers, and avoid legal issues. Businesses operating in heavily regulated industries must align their maintenance approach with these requirements to ensure smooth operations.
Steps for Selecting a Maintenance Strategy
Picking the right maintenance strategy takes planning and a clear understanding of your equipment, resources, and long-term goals. Here’s a step-by-step approach to help you build a structured and reliable system that keeps everything running smoothly.
-
Lay the Groundwork
Before diving into any maintenance strategy, take a step back and assess what you have. Look at your team’s skills, available resources, and existing workflows. Form a group to set objectives and provide direction, ensuring the plan aligns with your company’s needs.
-
Identify Critical Assets
Not all equipment requires the same level of attention. Conduct a criticality analysis to determine which assets are the most important for operations and what risks come with their failure. This step helps prioritize maintenance efforts where they matter most, preventing unnecessary downtime.
-
Compare Costs and Benefits
Once you’ve identified the most important assets, weigh the costs and benefits of different maintenance approaches. Consider preventive, predictive, and reactive strategies based on how each option impacts performance, longevity, and expenses. The goal is to find a balance between cost efficiency and reliability.
-
Put the Plan into Action
With a strategy in place, introduce new tools, schedules, and workflows. Provide thorough training so your team understands their roles and feels confident handling maintenance tasks. A smooth transition ensures the plan is followed consistently and without confusion.
-
Track Progress and Adjust as Needed
A maintenance strategy isn’t a one-time setup—it needs to evolve. Regularly collect data, analyze performance trends, and make adjustments where necessary. If something isn’t working as expected, fine-tune your approach to improve efficiency and reduce unexpected failures.
How to Improve Maintenance Strategy
-
Equipment Management
- Assess Asset Inventory: Start by taking a close look at all the equipment you own. Keeping track of each asset ensures you understand what you have, its condition, and its value. This step lays the foundation for any maintenance planning.
- Evaluate Equipment Criticality: Not all equipment is the same in terms of importance. By identifying which assets are critical to your operations, you can prioritize maintenance and prevent disruptions. This helps you focus your resources where they’ll have the most impact.
-
Preventive Maintenance
- Schedule Regular Inspections: Setting up a routine for inspecting your equipment helps you spot potential problems early. Regular checks allow you to address minor issues before they turn into costly repairs.
- Carry Out Routine Maintenance Tasks: Develop a list of standard tasks that should be carried out on a regular basis. These tasks, like cleaning or lubrication, help to keep equipment in good condition and reduce the likelihood of unexpected breakdowns.
-
Maintenance Planning
- Use Checklists for Work Orders: Detailed checklists are an excellent tool for making sure all maintenance tasks are completed properly. Work orders with clear steps help technicians stay on track and ensure no part of the process is overlooked.
- Plan Ahead for Maintenance: Don’t wait for something to break before addressing it. Plan your maintenance activities in advance to reduce disruptions and avoid emergency repairs. This proactive approach helps maintain smooth operations and prevent costly downtime.
-
Resource Management
- Provide Ongoing Training: Keeping your team well-trained is important for smooth maintenance operations. Regular training ensures your staff is updated on best practices, new equipment, and safety protocols, which helps them perform their tasks efficiently.
- Ensure Resource Availability: Make sure you have the right tools, spare parts, and personnel available when you need them. Having the proper resources at hand ensures that maintenance can be carried out without delays, avoiding bottlenecks and downtime.
-
Technological Integration
- Implement CMMS Software: Using a Computerized Maintenance Management System (CMMS) can help you track, schedule, and manage all maintenance activities. This software streamlines the process, reduces human error, and keeps records for future reference, making it easier to stay on top of maintenance tasks.
- Automate Maintenance Processes: Automation can significantly improve efficiency. Setting up automated alerts for maintenance tasks or even automating parts of the process helps reduce manual work and ensures nothing is missed. This can lead to more consistent maintenance and fewer service disruptions.
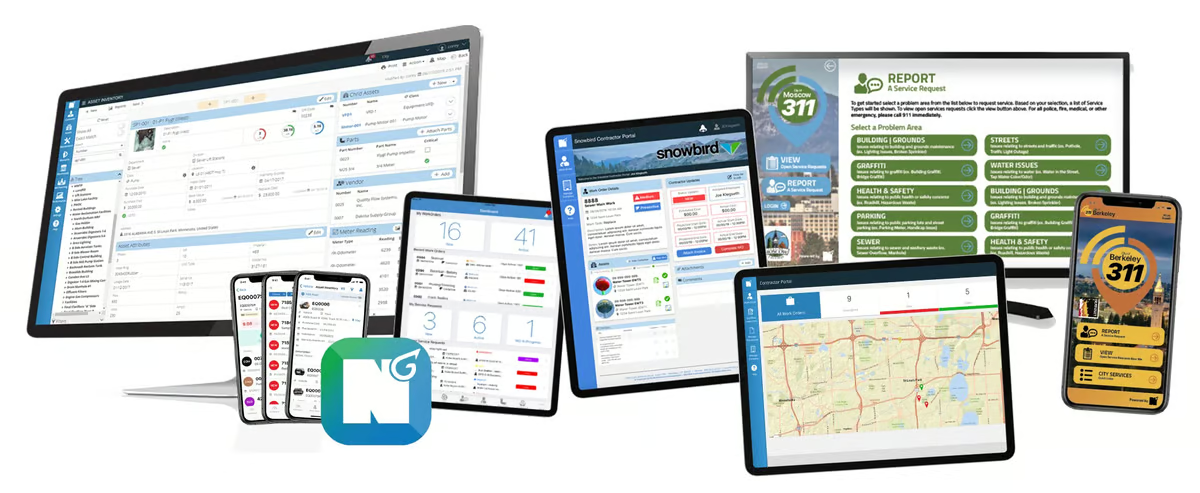
Ready to Learn How CMMS Works?
If you’re looking for a way to make maintenance easier, CMMS software might be just what you need.
Learn More About What is CMMS
Why Good Maintenance Strategy are Essential for CMMS Software
Even the best CMMS software will mean nothing without good maintenance strategies. That’s because good practice helps amplify your system and brings all kinds of benefits like:
- Improved efficiency: When you maintain CMMS software well, it can function at its peak. That way, you can ensure that work orders, preventive maintenance schedules, and asset management tasks all flow seamlessly. This efficiency leads to time-saving spent on administrative tasks and increases overall productivity.
- Reliability: A well-maintained CMMS software provides more accurate and up-to-date information. This will allow your organizations to make better and more informed decisions regarding their maintenance operations. This practice in CMMS software will minimize downtime and reduce costs.
- Cost-effectiveness: You can avoid potential issues and costs with poor software maintenance by implementing good maintenance strategies. Some problems you can avoid include system crashes, data loss, or security breaches.
These issues can be costly and time-consuming to fix. So, preventing them from occurring can save organizations time and money in the long run.
NEXGEN CMMS Bring Better Asset Management and Operations
Proper maintenance of your maintenance management software is an integral part of ensuring optimal asset management and seamless maintenance operations. NEXGEN CMMS software provides the tools necessary for efficient maintenance management, its success hinges on how well you and your maintain the system.
These practices will help your organization avoid potential pitfalls such as data loss, system crashes, or inefficiencies in operations. This way, you can have full confidence in your system and keep operating your asset management and maintenance.
These best practices are there to maintain the status quo and continually improve and adapt your maintenance management system to fit your evolving business needs.
NEXGEN Makes Maintenance Easier
With the right maintenance strategy, NEXGEN CMMS software can continue to be a powerful asset in your organization’s maintenance strategy, offering significant benefits for years to come.