A Computerized Maintenance Management System (CMMS) is a helpful tool that simplifies maintenance tasks and keeps manufacturing operations on track. It acts as a central place to store all maintenance-related information, including equipment details, schedules, and inventory. With a CMMS, manufacturers can plan ahead for maintenance and even predict when issues might occur. This helps reduce unexpected breakdowns and keeps equipment running smoothly. The system also provides reports that can be used to stay compliant with regulations and evaluate performance.
In discrete manufacturing, where production involves different types of equipment and frequent changes in schedules, a CMMS becomes even more useful. It helps organize the maintenance of various machines and allows manufacturers to adapt quickly to production shifts. By providing real-time data and helping plan maintenance in advance, it reduces downtime, improves efficiency, and ensures products are made to a high standard without unnecessary delays.
In this blog, we’ll take a closer look at how CMMS can transform discrete manufacturing, making maintenance simpler and operations more productive. Without waiting further, let’s get started.
How CMMS Supports Discrete Manufacturing
Aspect | CMMS in Discrete Manufacturing |
---|---|
Equipment Tracking | Tracks every piece of equipment individually, giving you a clear view of their status, usage history, and performance. This helps ensure timely interventions and reduces the risk of overlooking assets. |
Maintenance Planning | Handles the diverse maintenance needs of different machines, each with unique schedules, requirements, and service intervals. It ensures that preventive tasks are done on time, avoiding unplanned breakdowns. |
Flexibility | Adapts to regular changes in product designs or production setups. Whether it’s reconfiguring assembly lines or introducing new machines, the system adjusts seamlessly to the evolving needs. |
Regulatory Tracking | Maintains detailed logs of all maintenance activities, creating a reliable trail to meet industry standards. It helps in passing audits and complying with safety and operational regulations. |
Downtime Reduction | Assists in organizing maintenance windows and equipment changeovers to minimize disruptions. By streamlining processes, it ensures production runs smoothly with fewer interruptions. |
What is Discrete Manufacturing?
Discrete manufacturing refers to the production of individual, distinct items that can be easily separated into parts. Unlike process manufacturing, where products like pharmaceuticals or paper are created in a continuous flow and can’t be broken down into individual pieces, discrete manufacturing deals with products that consist of various components. These items are often assembled using parts like nuts, bolts, screws, and brackets, and the final product can be disassembled and recycled into its original parts once it reaches the end of its lifecycle.
For example, consider things like toy planes, actual airplanes, cars, or furniture. These are all examples of discrete manufacturing because they’re made up of individual pieces that can be put together and taken apart. On the other hand, items from process manufacturing, like chemicals or gas, are produced in a continuous process, and you can’t separate them into individual components once they’re made.
In discrete manufacturing, each product is typically unique or made in small batches, allowing for more flexibility in production and often a higher level of customization. This makes it easier to track, repair, or replace specific components, which is where a CMMS (Computerized Maintenance Management System) can play a significant role in helping manufacturers maintain their equipment and manage production efficiency.
Maintenance in Discrete Manufacturing
Discrete manufacturing is a production process that is driven by customer orders. Unlike make-to-stock models, which produce goods in anticipation of future demand, discrete manufacturing is based on the make-to-order principle. This means each product is made individually, often requiring a detailed bill of materials (BOM) to ensure the right raw materials and components are available. Industries like aerospace and automotive rely heavily on discrete manufacturing processes to create their specialized products.
One of the main advantages of discrete manufacturing is its ability to minimize waste, which aligns with lean manufacturing principles. However, while this model offers efficiency in many ways, it comes with its own set of challenges, especially when it comes to maintenance. Let’s break down some of these challenges.
-
Inventory Management
In discrete manufacturing, managing inventory is super important. Since each product is unique, the production process relies on a bill of materials (BOM), which lists all the materials needed for each specific product. This means that factories that produce a variety of products must keep a large stock of different materials on hand. Managing these inventories can be tricky, especially when the production style varies from high-volume, low-complexity items to low-volume, high-complexity products.
When dealing with high-volume production, inventory management becomes even more difficult. If the inventory is not managed well, it can cause a ripple effect on both the manufacturing and maintenance processes. For instance, if the necessary spare parts for machines or equipment aren’t readily available, it can lead to unexpected downtime. Technicians may find themselves waiting on the shop floor, unable to complete repairs, which slows down the entire production line. Prolonged downtime not only hampers productivity but also increases maintenance costs.
By staying on top of inventory management and ensuring that the right materials are available when needed, manufacturers can avoid unnecessary delays and keep their maintenance processes running smoothly. This proactive approach helps minimize disruption, making it easier to maintain the flow of production.
-
Production Capacity
In discrete manufacturing, maintenance planning can be tricky because of the challenges with production planning. One of the main reasons this is tough is that determining production capacity isn’t straightforward. Unlike continuous manufacturing where the process is repetitive, discrete factories often make a wide variety of products in different quantities based on customer orders. This means there’s no fixed daily or monthly output to rely on.
As a result, predicting the required production resources, including the assets and equipment, becomes complex, which makes it harder to plan for necessary maintenance activities. Without a clear picture of how much and what type of production will happen, maintenance teams can struggle to schedule their work efficiently.
-
Process Standardization
Another hurdle in discrete manufacturing is process standardization. Since each product can be so different, the processes for assembling, routing, and maintaining equipment can vary greatly from one production run to the next. Different assets, tools, and machines might need attention at different times. This variation adds an extra layer of complexity when creating standard operating procedures for maintenance teams.
Each production line may require its own set of maintenance schedules, making it difficult to streamline the process and ensure consistency. It’s a balancing act, but with careful planning, you can minimize downtime and ensure everything runs smoothly despite the differences in production processes.
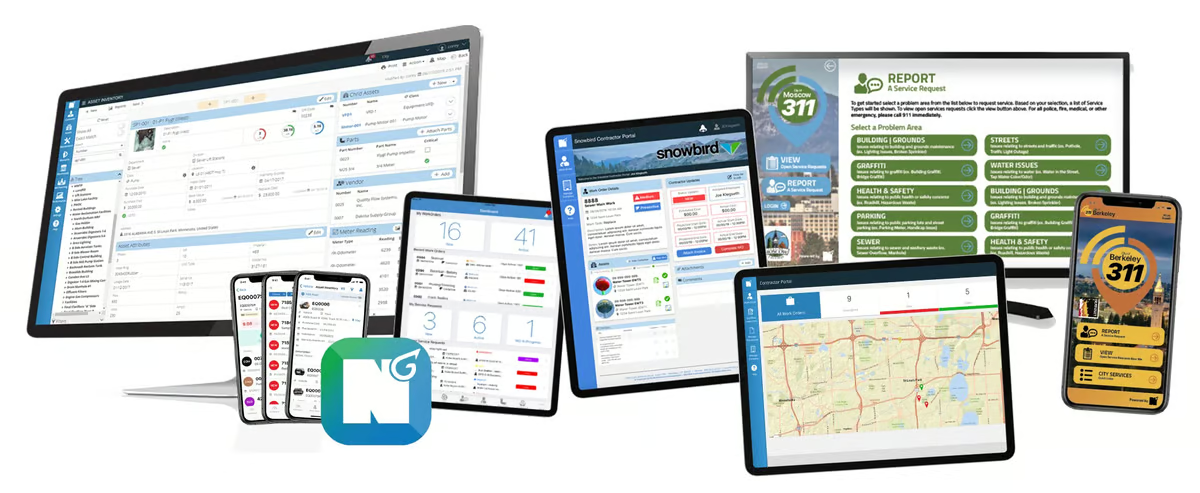
Ready to Learn How CMMS Works?
If you’re looking for a way to make maintenance easier, CMMS software might be just what you need.
Learn More About What is CMMS
CMMS Applications in Discrete Manufacturing
Managing equipment and maintenance is a major part of keeping things running smoothly in manufacturing. A CMMS helps make this job easier by supporting manufacturing in the following ways:
-
Production Line Maintenance
A CMMS helps monitor the condition of machines on the production line, spotting issues early before they become bigger problems. It also helps schedule regular maintenance, reducing the chances of unexpected breakdowns and keeping the production line running without delays.
-
Equipment Lifecycle Management
A CMMS keeps track of each piece of equipment from the moment it’s bought until it’s no longer in use. This helps manufacturers decide when to repair, replace, or upgrade equipment. By looking at things like repair costs and how often equipment breaks down, they can make smarter choices about whether to keep or replace machinery.
-
Quality Control
A CMMS ensures that equipment stays within required tolerances, helping maintain high-quality production. It also keeps track of maintenance records, which makes it easier to trace and fix any defects quickly. This helps keep the production process smooth and ensures products meet quality standards.
-
Collecting and Storing Data for Smarter Maintenance
In a discrete manufacturing environment, keeping track of maintenance can be challenging. A good CMMS (Computerized Maintenance Management System) that stores data in the cloud can make a significant difference. With this system, you’ll be able to capture useful information on how your assets are performing in real-time. You may not always notice trends in your daily operations, but a CMMS with strong reporting features can provide you with important insights, helping you identify patterns that can improve your maintenance planning.
For instance, with systems like NEXGEN, you can integrate with your CRM and other industry-specific software to streamline processes. Tools like NEXGEN CMMS can connect assets to service providers and track parts inventory, making it easier to keep things running smoothly.
-
Predictive Maintenance for Better Efficiency
For many discrete manufacturing plants, sticking to a routine preventive maintenance schedule might not be the most efficient option. The irregular nature of orders and asset usage means traditional maintenance schedules can often lead to unnecessary checks or missed opportunities for timely fixes. That’s where predictive maintenance comes in. By monitoring the actual condition of equipment, you can perform maintenance based on how the asset is performing, not just a set timeline. This approach helps save time and resources, ensuring you’re only maintaining assets when necessary, rather than on a fixed schedule.
-
Connecting Your Workforce for Smarter Operations
A CMMS helps bring together your manufacturing and maintenance teams in ways that can boost productivity. It can automate work orders, meaning tasks get assigned and tracked without extra manual steps. Additionally, with real-time updates from the shop floor, your teams are always in the loop. You can set notifications for things like inventory levels, procurement needs, asset lifespans, and even unexpected downtime. By linking everything together in one system, you ensure that your team has the tools they need to keep operations running smoothly, saving you time and preventing bottlenecks.
How CMMS Supports Maintenance Management in Discrete Manufacturing
CMMS (Computerized Maintenance Management System) provides a range of tools and features designed to help discrete manufacturing businesses handle maintenance tasks more efficiently. Here’s how it can make a difference:
Asset Management
- CMMS helps maintain an asset register and ensures both physical and digital asset verification.
- RFID tags and QR code scanning are used for real-time asset tracking, making it easier to keep tabs on equipment.
- IoT sensors monitor the health and performance of assets, providing continuous updates on their condition.
- CMMS centralizes the process of managing asset depreciation, maintenance schedules, and asset disposition.
- Geo-tagging features restrict access to sensitive asset data, enhancing security and control.
- Dashboards in CMMS allow for the easy visualization and analysis of maintenance data, helping track performance over time.
Preventive Maintenance
- CMMS supports condition-based monitoring using IoT sensors and data analytics to prevent unexpected equipment failures.
- A preventive maintenance calendar can be scheduled up to 52 weeks in advance, reducing the risk of unscheduled downtime.
- By analyzing both preventive and breakdown maintenance data, CMMS helps in deciding whether an asset should be repaired or replaced.
- CMMS calculates MTBF (Mean Time Between Failures) and MTTF (Mean Time To Failure) to optimize maintenance schedules and predict equipment reliability.
- FMEA (Failure Modes and Effects Analysis) is used to identify potential failure modes and prioritize maintenance tasks accordingly.
Operations Management
- CMMS streamlines daily maintenance activities, simplifying routine tasks and operations.
- Checklists and standardized procedures help ensure consistency in maintenance practices.
- Integration with production systems ensures that maintenance schedules are aligned with production needs, reducing downtime.
- CMMS provides real-time visibility into equipment status and ongoing maintenance activities, supporting more informed decision-making.
Issue and Ticket Management
- CMMS allows the creation of maintenance tickets with a simple QR code scan using mobile devices, making the process quick and accessible.
- Tickets can be assigned to internal staff or external vendors, and progress is tracked through a centralized ticketing system.
- Each ticket is prioritized based on the severity of the issue, with turnaround times (TAT) set to ensure timely resolution.
- The system enables smooth communication and collaboration between maintenance teams and other stakeholders, ensuring efficient issue resolution.
- If a ticket is not completed within the expected TAT, it can be escalated for faster action.
Work Order Management
- CMMS streamlines the generation, assignment, and tracking of work orders to ensure timely resolution of maintenance tasks.
- This system helps allocate resources efficiently, improving the overall workflow and productivity of maintenance teams.
- By improving the efficiency of work order management, CMMS contributes to a smoother operation and quicker response times.
Inventory Management
- CMMS tracks spare parts inventory and usage, helping ensure that essential parts are always available for maintenance tasks.
- The system optimizes inventory levels to avoid both overstocking and shortages, improving cost management and procurement processes.
- With the right parts readily available, maintenance tasks can be completed on time without unnecessary delays.
Permit to Work Management
- CMMS helps manage hot and cold work permits, as well as gate passes, ensuring that all necessary approvals are in place before work begins.
- The system tracks the status of permits, including approval and expiration dates, to avoid any compliance issues.
- Integration with safety management systems ensures that all work adheres to regulatory requirements, improving safety in the workplace.
- CMMS promotes collaboration between different departments for smooth permit issuance and approval processes.
Analytics and Reporting
- CMMS offers advanced analytics tools to analyze key performance indicators, helping track the effectiveness of maintenance strategies.
- The system identifies trends and patterns in maintenance data, enabling improvements in processes and decision-making.
- Data-driven insights allow manufacturers to optimize maintenance efforts, reduce costs, and improve equipment reliability over time.
How to Pick the Perfect CMMS for Your Manufacturing Needs
The first thing to think about when choosing a CMMS is the size and complexity of your operation. If you’re running a large or complex manufacturing setup, you’ll need a solution that can grow with you. Bigger operations often need a system that can adapt as things change. For discrete manufacturing, you’ll want a system that can handle frequent equipment changes. On the other hand, if you’re in process manufacturing, you should focus on features that help you meet strict regulations and compliance standards.
Don’t forget to consider your budget and what kind of return on investment (ROI) you expect. It’s important that the CMMS solution fits within your financial plan and offers value over time. By keeping these factors in mind, you can choose a system that not only works well now but also supports your goals down the road.
Use NEXGEN to Automate Manufacturing Maintenance
NEXGEN offers a range of integrations, which will help you standardize procedures, manage safety and regulatory compliance. Interested in seeing how NEXGEN can optimize your discrete manufacturing operations?